在市城乡一体化示范区(高新区),当晨光熹微,三门峡戴卡轮毂制造有限公司的智慧云工厂已全速运转。物流车穿梭于WMS职能仓储立体货架间,5G+AI质检系统以每秒200帧的速度扫描轮毂表面,数据大屏上跃动的数字见证着传统制造企业的蜕变:2024年营业收入突破17亿元,自主品牌销量三年激增300%,人均产值跃升至162万元。一组组逆势上扬的曲线,勾勒出“三大改造”赋能下的智造新图景。 数字基因重塑生产逻辑 “这个智能决策中枢,就是工厂的‘最强大脑’。”站在5G智慧云工厂调度指挥中心,正在介绍情况的运营管理中心经理助理李海波指向数字孪生平台。透过大屏,520台联网设备、300块能源仪表的实时数据在此交汇,形成覆盖生产全流程的数字神经网络。自2021年启动的1.03亿元数字化转型工程,不仅建成七大5G场景应用,还使生产节拍缩短23%,单只轮毂能耗下降15%。 在机加车间,技术部经理李颖展示着最新研发的AI自适应控制系统。通过“5G+工业互联网”平台,CNC机床能根据铝材特性自动调整参数,将加工精度控制在0.02毫米以内。“过去老师傅需半小时调试的参数,现在系统1分钟就能完成。”这种智能进化使产品综合合格率突破94%,推动企业从规模扩张向质量效益转型。 绿色智造激活产业链动能 清晨7点,满载铝液的专用运输车从恒康铝业驶入厂区。通过铝水直供项目,企业每年减少合金重熔燃料成本2000万元,实现碳减排1万吨。“这不仅是成本账,还是生态账。”运营总监魏要星算着绿色转型的“双赢账”,通过与上下游构建循环经济体系,区域铝产业链综合效益提升了18%。 熔炼车间采用全球领先的蓄热式燃烧技术,将铝液保持在720℃恒温,并通过余热回收系统将能源利用率提升至92%。财务副总李红强透露,通过智能仓储系统和云端产能协同平台,存货周转率同比提升35%,资金使用效率显著优化。这种全价值链的绿色再造,推动企业利润在2024年实现42%的跨越式增长。 创新引擎驱动新质生产力 走进企业技术中心,北航、浙大科研团队正攻关新一代铝基复合材料。通过“揭榜挂帅”机制,企业近三年转化科技成果27项,其中与西安电子科技大学合作的智能检测系统,使质检效率提升6倍。目前,企业研发投入强度达4.8%,拥有专利技术56项,数字化人才占比突破30%。 创新势能正转化为市场竞争力。今年年初,已有15万只轮毂发往日本、欧盟市场,自主品牌产品在国际展会上收获超2亿元订单。企业打造的“产销研一体化”平台,通过大数据分析精准捕捉市场需求,使新产品研发周期缩短40%,个性化定制产品占比提升至25%。 站在智慧工厂参观通道,智能制造场景尽收眼底:机械臂精准抓取、AI图像识别传输链流动、云端系统实时调度……这座曾以传统铸造闻名的工厂,如今正以每分钟下线12只轮毂的“戴卡速度”,书写资源型城市转型新篇章。随着“三大改造”深入推进,戴卡轮毂正朝着“全球一流铝轮毂智能制造基地”目标阔步前行,为培育新质生产力、建设现代化三门峡注入强劲动能。 ( 编辑:tln ) |
“数字基因·智造革命”——从车间到云端的转型实践系列报道之九
戴卡轮毂:传统制造工厂“智慧”蝶变
本报记者 何东升
来源: 发布日期:2025-04-28 打印
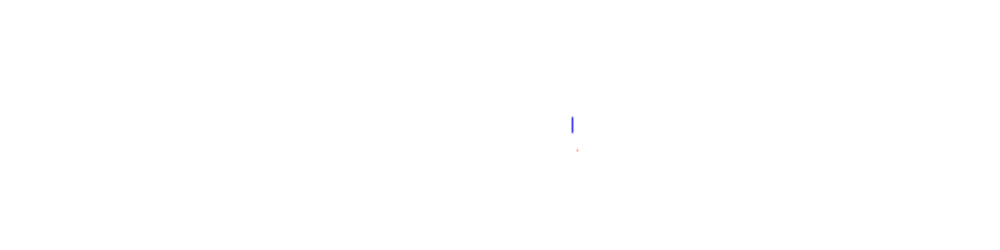